Industrial automation has been in use for centuries, in the form of technology like water wheels and windmills — but we have come a long way. Today, innovations that once seemed like science fiction are now commonplace throughout the supply chain. These technologies can help reduce labor and improve safety and efficiency while also freeing up people to work on more complex and creative tasks. Modern warehouse automation, backed by increasingly innovative software, is fueling a more optimized and streamlined supply chain.
What is Warehouse Automation?
Warehouse automation involves the use of technology tools — both equipment and software — to perform both manual and complex tasks traditionally done by human workers. These technologies can range from basic tools that reduce manual labor, such as automatic palletizers, to AI-driven solutions that enable fully automated operations with minimal human involvement. The integration of automated processes and technologies enables supply chain managers to reduce costs and increase safety while also enhancing accuracy and accelerating customer order fulfillment.

How Does a Fully Automated Warehouse Work?
In a fully automated warehouse or other logistics environment, high-tech machines, robotic equipment, and specialized software work seamlessly to manage every stage of the supply chain workflow, from receiving income goods to shipping out orders. In many cases, human involvement and intervention are minimal, with the exception of maintenance and repairs. Items are scanned upon arrival, sorted and stored using automated technology, and then retrieved, picked, and packed when needed. Advanced software tools, meanwhile, ensure that all operations are tracked and managed in real time — providing key insights and analytics along the way.
What are the Three Levels of Warehouse Automation?

Semi-Automated Warehouses
Semi-automated warehouses are hybrid environments, with human workers and assistive automated technology working in tandem. For example, managers may implement conveyor belts, automated sorting systems, or pick-to-light systems to enhance the productivity of warehouse associates. This level of automation can be ideal for smaller operations in which productivity assistance is useful but there is no need or desire to replace certain tasks performed by human workers.
Fully Automated Warehouses
Fully automated warehouses rely more heavily on advanced robotics, AI-driven software, automated guided vehicles, and automated storage and retrieval systems. The focus is on precision and efficiency, with minimal human intervention.
Lights-Out Warehouses
Lights-out warehouses represent the true pinnacle of warehouse automation. Because these facilities operate entirely without human intervention, there is theoretically no need for lights, human-friendly climate control, or other amenities needed in an environment that caters to workers. From stocking inventory to fulfilling customer orders, robots and AI technology handle everything — often 24 hours a day, seven days a week.
Types of Automation Solutions for Warehouses
The typical makeup of an automated facility comprises a wide variety of technology solutions, and while not every facility may need each of these components — and while this list does not cover each and every type of automated innovation available — it is helpful to be familiar with the following solutions:
- Workflow Management Software: This software automates task scheduling and monitoring, ensuring smooth coordination between systems and workers.
- Automated Storage and Retrieval Systems (AS/RS or ASRS): AS/RS solutions store and retrieve inventory using cranes, shuttles, or carousels, maximizing space and efficiency.
- Pick-to-Light/Put-to-Light Systems: These systems use light indicators to guide workers to the correct inventory locations, reducing errors and speeding up the picking process.
- Automated Guided Vehicles (AGVs): AGVs transport goods within the warehouse along predefined paths, improving material handling efficiency.
- Autonomous Mobile Robots (AMRs): Unlike AGVs, AMRs use sensors and mapping technology to navigate dynamically, offering more flexibility in handling tasks.
- Voice Picking: Voice-directed systems guide workers through tasks using audio instructions, improving speed and reducing training time.
- Conveyor and Sortation Systems: Conveyors and sorters move products through the warehouse quickly and efficiently, streamlining order fulfillment.
- Warehouse Management System (WMS): A WMS tracks inventory, coordinates operations, and optimizes warehouse workflows.
- Warehouse Execution System (WES): A WES integrates with WMS and other systems to manage real-time operations, ensuring efficient resource use.
Examples of Warehouse Automation
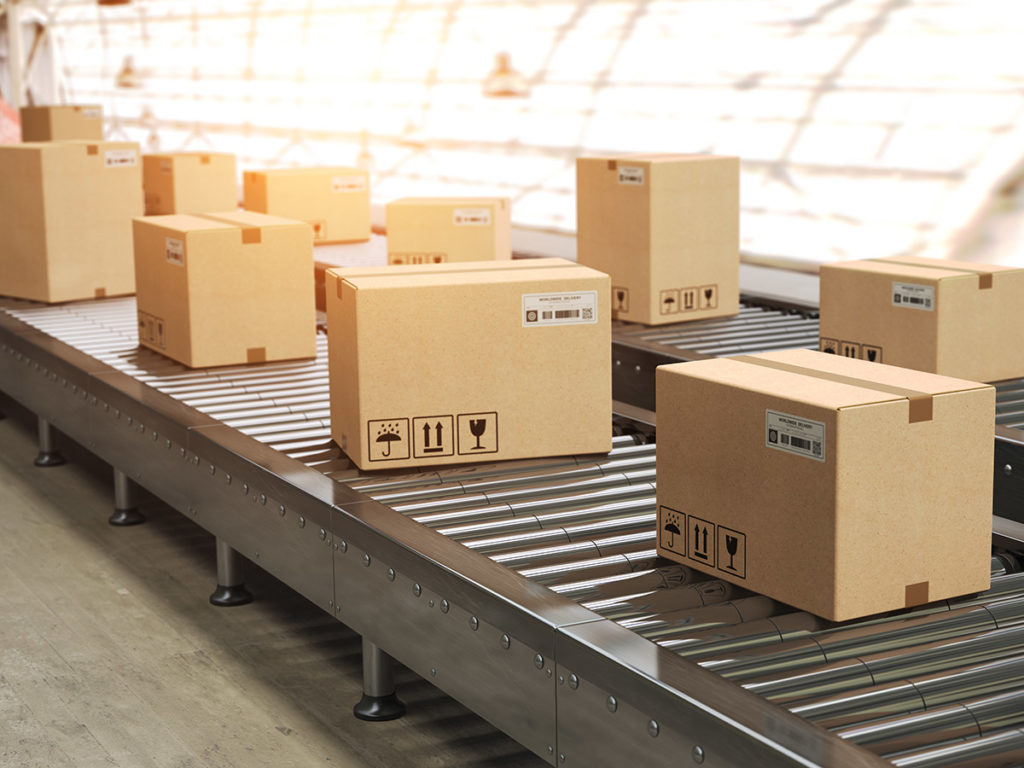
Automated Order Fulfillment for E-commerce
A bustling e-commerce facility receives hundreds of orders per hour. Automated processes begin the very moment an order is placed. Software identifies the item or items needed and their precise location within the facility. An Automated Storage and Retrieval System (AS/RS) quickly retrieves the items, while robots bring them to a packing station. Robotic equipment assembles shipping boxes and packs the items, and a conveyor moves the sealed package to a sorting area where it can be directed to the correct shipping dock. Little if any human involvement is needed — and the order is typically fulfilled with unparalleled speed and accuracy.
Inventory Management for a Distribution Center
A retail distribution center handling many thousands of stock-keeping units (SKUs) employs automated barcode scanners to track inventory levels in real time. When a new shipment arrives, scanner-equipped conveyors sort products and transport them to the appropriate storage zones, where they can be quickly and accurately placed in high-density racking systems that prioritize space utilization. The system instantly updates inventory records and enables real-time tracking for when replenishments are needed.
Grocery Fulfillment Center with Perishable Items
In a warehouse storing fresh fruits and vegetables as well as frozen goods, time-sensitive inventory management is critical. Robotic equipment armed with temperature sensors transports items to the appropriate temperature-controlled zones, and orders are prepared using pick-to-light systems that guide human workers. Conveyors then transport finished orders to trucks with built-in refrigeration to keep perishables fresh during transport.
Benefits of Warehouse Automation
The potential supply chain scenarios in which warehouse automation can improve accuracy, enhance safety, reduce costs, and accelerate order fulfillment are virtually limitless. Here are just three examples of efficient facility automation in action:
The clear advantages of automation are numerous. Because automated systems work faster and more consistently than human workers, they increase productivity and overall efficiency. They also limit the risk of injury, either from repetitive stress such as lifting, or from preventable accidents. Other benefits include:
Increased Efficiency
Automation reduces the need for manual effort, speeding up processes and operations overall. This results in a more optimized supply chain.
Improved Accuracy
While automated systems are not perfect, they are also less likely to make the types of mistakes that humans might, improving both inventory management and order fulfillment. This enhances both customer satisfaction and minimizes the need for reverse logistics.
Cost Savings
While startup and ongoing investments in automation can be considerable, automation reduces labor costs and operational expenses (and therefore, Total Cost of Business) over time.
Scalability
Automated systems can easily scale to handle increased demand, without the need to hire additional workers or content with labor shortages.
24/7 Operations
Fully automated warehouses can operate around the clock, further boosting productivity and favorable business results.
Disadvantages of Warehouse Automation
Despite its many benefits, automation also comes with its own set of challenges, and over-reliance on technology can quickly lead to disruption when that technology fails to operate as intended. Other potential pitfalls include:
High Startup Costs
Although automation can pay for itself over time, it can require significant upfront capital that may not be feasible for all enterprises.
Maintenance Requirements
Automated systems need repairs, maintenance, and upgrades, which can delay operations
Workforce Disruption
The implementation of automation leads to job displacement, which requires investments in more skilled workers and can also lead to reputational risk.
How to Implement Warehouse Automation

Transitioning to an automated system typically begins with a comprehensive assessment of existing supply chain operations. This can include the identification of bottlenecks and inefficiencies to determine which areas of the process can benefit from automation. An understanding of goals is also crucial — whether it is minimizing reliance on human labor, reducing order processing times, improving inventory and order accuracy, or all of the above and more.
Selecting the right technologies is crucial, dependent on factors that include budget, warehouse layout, and current and future needs.
Selecting the right technologies is crucial. Consider your budget, warehouse layout, and future needs. A phased implementation approach can help minimize disruptions, allowing your team to adapt gradually. Lastly, ongoing monitoring and optimization ensure that your automated systems continue to meet your business objectives. Other priorities include:
- Planning the transition to ensure minimal disruption to ongoing operations
- Providing employees with the necessary training to implement, work alongside, and/or manage and maintain automated systems
- Continually monitoring and optimizing both the implementation and the ongoing performance of automated systems to ensure that adjustments can be made as needed
Supporting Intelligent Warehouse Automation with iGPS Plastic Pallets
A crucial part of implementing warehouse automation involves the use of packaging and equipment that will neither damage nor be damaged by the automated system. It is also important to use equipment that allows data to be easily read by automated systems.
While they have been viewed as a reliable mainstay in the logistics sphere for decades, wood pallets are actually a common source of issues within the supply chain. Wood pallets tend to break and shed pieces and splinters. Because of their malleability and ability to absorb moisture, wood pallets can warp, vary in weight, and change in size depending on their environmental conditions. Synergy between the components of an intelligent automated warehouse system can be enhanced by the use of durable plastic pallets. Only the recyclable, lightweight iGPS plastic pallet has features that integrate seamlessly with all types of warehouse automation:

Intelligence
The iGPS pallet incorporates smart features like GS1-standardized Global Returnable Asset Identifiers (GRAI) and RFID chips that make it readable by all types of automated systems. This improves traceability and allows accurate data capture at all points throughout the supply chain.

Consistency
The iGPS plastic pallet does not absorb moisture and is not subject to the size and weight variations of wood platforms, which can cause automated machinery to jam or miscalculate. A precisely engineered plastic pallet helps any automated system deliver consistently high performance.

Durability
iGPS plastic pallets are up to 35 percent lighter than wood block pallets and therefore reduce the fuel needed to transport products. Since iGPS operates a closed-loop plastic pallet pooling model, there is no need to worry about plastic escaping into the environment.

Standardization
The iGPS plastic pallet is fully compliant with Consumer Brands Association (CBA) specifications. That means that iGPS plastic pallets can be easily handled by existing warehouse equipment as well as by newly manufactured automated warehouse systems.
In a single package, iGPS provides a shipping platform that capably supports intelligent warehouse automation in any distribution center. The consistent, durable iGPS plastic pallet is fully equipped to maximize the efficiency gains from implementing warehouse automation; to reduce Total Cost of Business; and to maximize swift return on investment.
Frequently Asked Questions
What is the objective of warehouse automation?
The objective of warehouse automation is to streamline operations by reducing manual labor, improving efficiency, and enhancing accuracy in tasks such as inventory management, order fulfillment, and shipping. By leveraging technology like robotics and software systems, enterprises can minimize errors, optimize resource use, and handle increasing demand with greater speed and reliability.
What is the role of a warehouse automation specialist?
A warehouse automation specialist designs, implements, and maintains automated systems within a warehouse. They assess operational needs, recommend suitable technologies, and ensure seamless integration of hardware and software. Additionally, they monitor system performance, troubleshoot issues, and train staff, ensuring that automation solutions align with business goals and function efficiently over time.
What are the key What is warehouse automation software?
Warehouse automation software refers to digital tools that coordinate, optimize, and manage automated processes within a warehouse. These systems include Warehouse Management Systems (WMS), Warehouse Execution Systems (WES), and other workflow software. They enable real-time tracking, task prioritization, and efficient resource allocation, ensuring smooth operations and effective integration with physical automation technologies
What type of pallets are best for warehouse automation?
Plastic pallets like the iGPS Pallet are ideal for warehouse automation due to their consistency, durability, and precision. They ensure the smooth operation of automated systems by minimizing malfunctions and downtime. Features like four-way entry, uniform construction, and high load capacity make them perfect for AS/RS. While plastic is generally best, aluminum or recycled wood may suit specific needs. Ultimately, the best pallet depends on individual equipment requirements and budget.