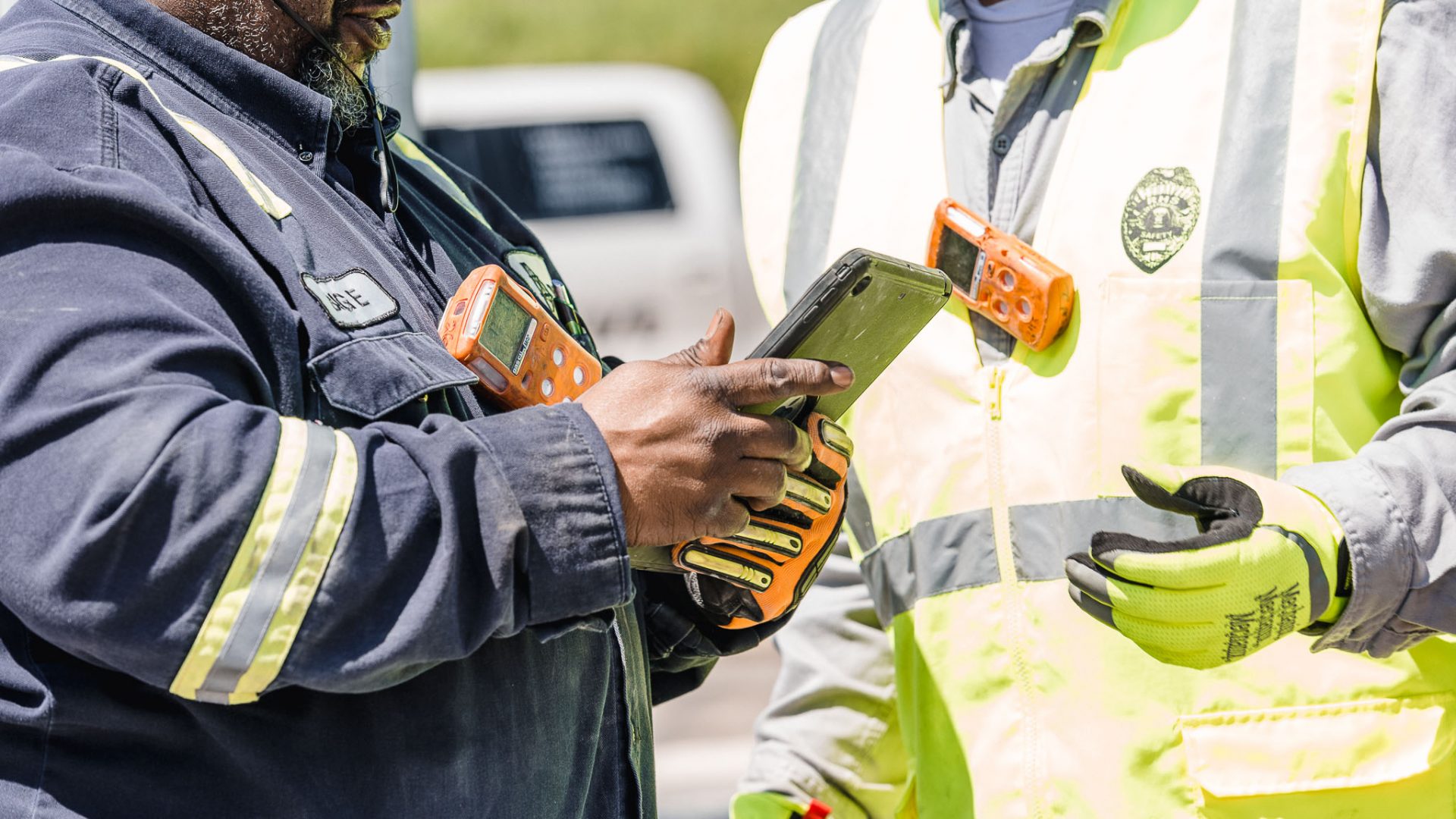
Safety
At EQT, we place the highest priority on the safety of our workforce — both for employees and contractors — as well as in the communities where we work.
Zero is Possible if we FOCUS on Safety
At EQT, we are committed to creating an environment where Zero is Possible. An environment where we continuously FOCUS on what it takes to keep us all safe, healthy and injury free. Whether you are employee, contractor, or subcontractor YOU are our most valuable asset.
We recognize the importance of providing policies, procedures and tools to keep everyone safe, but more importantly, we want you to understand WHY these are in place and why they are important.
At EQT, we appreciate everyone’s contributions to our culture of safety and cooperation in following our safety requirements to make our workplace healthy and injury free.
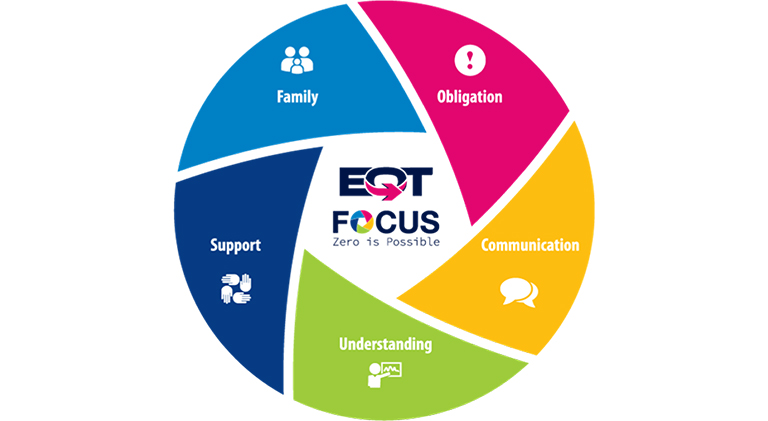
Our F-O-C-U-S on Safety
F is for Family.
Family is about expanding our connections and caring for the people here at work and at home, and treating everyone as our family.
O is for Obligation.
Each one of us has an obligation to perform our jobs efficiently, effectively and safely in a manner that protects the health and safety of us and those around us.
C is for Communication.
Communication is engaging in respectful conversations that focus on our common goals and values.
U is for Understanding.
Understanding is being aware of our safety goals and how we can each contribute towards achieving them.
And, S is for Support.
Support is working together to create an environment where Zero is Possible. A safe working environment to ensure we all return home safely to our families.
Workforce Safety Management Overview
All EQT employees and contractors are accountable for ensuring a safe working environment and culture. Being accountable means never taking shortcuts with safety. EQT’s workforce is empowered with “stop work” authority, which means every employee and contractor has the authority and the obligation to immediately stop work if they question the safety of the work being conducted — both in the office and in the field.
Contractor Safety – One Team
Every service company who we contract workers with must mirror EQT’s commitment to safety. EQT uses ISNETWorld® — a third-party online platform for monitoring safety metrics, programs, performance and to establish minimum safety requirements — to qualify contractors before they obtain authorization to begin work for EQT.
EQT also maintains a contractor safety orientation requirement. EQT contractor safety orientation completion must be documented for everyone (contractors and subcontractors) that work on EQT premises. The orientation is required annually or when changes occur to the EQT Contractor Safe Work Rules. In addition, a separate site or project specific safety orientation may be required.
Driving Safety
Our Safe Driving Leadership Team, consisting of representatives from Human Resources, Safety and several business units, develops and updates policies, such as Fleet Safety Procedures, that prioritizes the safety of our employees, contractors and local communities. EQT is committed to working with local communities and our partners to improve road safety in the locations where we operate.
We also help keep our drivers safe by limiting their journeys, enforcing our road safety requirements and using stop work authority when there is a question of safe conditions. In addition, employees must undergo a series of training programs including behind-the-wheel training and defensive driving modules and demonstrate safe driving skills through supervisor-observation sessions.
Emergency Preparedness
The most responsible emergency preparedness strategy prevents incidents from occurring. That said, EQT is prepared to respond quickly with detailed emergency procedures and trained professionals in the event of an incident. We combine planning with training and mock emergency exercises as well as regular updates to location-specific emergency response plans.
Safety Performance
We want our workforce (employees and contractors) to go home safely every day. By tracking and analyzing safety incidents, we can assess the effectiveness of our approach to safety management and enable continuous improvement. For example, we supplemented our OSHA (Occupational and Health Administration) metrics with a SIF (Serious Injury and Fatality) metric. The tracking of a SIF exposure rate allows us to better assess our safety program’s progress and to detect potential increases in risk.
EQT develops Safety Bulletins to address safety incidents and to share lessons learned within our workforce. These bulletins describe an incident and its impact to help inform, educate and prevent a future occurrence.